Ammonia cracking Purifier Unit
Soramair takes pride in being a leading designer and manufacturer of Ammonia Cracking Purifier Units. Our units, ranging from 5 Nm3/hr to 50 Nm3/hr with pressures from 0.5 Kg/cm2 to 5.5 Kg/cm2, are engineered to achieve a Dew point as low as –80 Deg Cent. The composition of the cracked ammonia boasts an impressive 75% Hydrogen and 25% Nitrogen.
Soramair takes pride in presenting its superior Ammonia Cracker Purifier Unit, designed to remove uncracked ammonia and moisture from cracked ammonia gas generated by our Ammonia Cracking Units. This essential equipment ensures the purity and dryness of your cracked ammonia, maximizing its efficiency and application potential across diverse industries.
Key Features of Soramair’s Ammonia Cracking Purifier Unit:
The unit is equipped with a 3-way inlet valve, 3-way outlet valve, and 2 Nos. 2-way valves for exhaust lines. These valves operate automatically, controlled by a timer, enhancing ease of operation. For Molecular Sieve regeneration, the temperature reaches 200 Deg. C uniformly, ensuring low power consumption, efficiency, and user-friendliness.
Major applications of Soramair’s Ammonia Cracker Purifier Unit
- On-site Generation of Cracked Gas: Generate pure Hydrogen and Nitrogen on-site, eliminating dependence on external suppliers and transportation costs. Ideal for applications like hydrogen brazing, heat treatment, and fuel cell technology.
- Nitrogen Generation Plants: Produce high-purity Nitrogen for various industrial processes, including food packaging, electronics manufacturing, and tire production.
- Pipe Manufacturing Industry: Utilize Hydrogen in the production of seamless steel pipes for enhanced strength and corrosion resistance.
- Sintered Brazing Industry: Generate clean Hydrogen atmospheres for brazing of critical components in aerospace and automotive applications.
- Galvanizing Plants: Employ Hydrogen in the galvanization process to improve the adhesion and corrosion resistance of zinc coatings..
- Automobile Industry: Utilize Hydrogen in the production of fuel cell vehicles and for brazing of automotive components.
- Heat Treatments: Generate controlled Hydrogen atmospheres for annealing, hardening, and other heat treatment processes in various industries.
Technical Specification of Soramair’s Ammonia Cracker Purifier Unit
- Flow ranges from 2 Nm3/hr to 20 Nm3/hr.
- Cracked Ammonia gas Having 75% Hydrogen and 25% Nitrogen
- The dew point Achieved up to -80 Deg Cent.
- Cracked ammonia gas pressure ranges from 1 kg/cm2 to 5 kg/cm2
- Two-vessel configuration with molecular sieves for continuous purification and regeneration.
- Fully automatic operation with timer-controlled valves and temperature indicators.
- Low power consumption and minimal maintenance requirements.
- Compact footprint for easy installation and integration.
Available Models of Soramair’s Ammonia Cracker Purifier Unit
- Molecular Sieve Towers (2 Vessels): Filled with highly adsorbent zeolite beads, these towers selectively remove uncracked ammonia and moisture from the cracked ammonia gas stream. One vessel operates in the purification cycle while the other undergoes regeneration.
- Three-Way Valves: Automatically control the flow of cracked ammonia gas and regeneration gas between the towers.
- Exhaust Lines: Vent desorbed moisture and uncracked ammonia during regeneration.
- Heating System: Heats the molecular sieves in the regeneration vessel to 200°C, desorbing and releasing the captured moisture and uncracked ammonia.
- Temperature Indicators: Monitor the temperature in each tower, ensuring optimal conditions for both purification and regeneration.
- Rotameter: Measures the flow rate of the purified cracked ammonia gas exiting the unit.
- Electrical Control Panel: Monitors and controls all unit operations, including valves, temperatures, and alarms.
Working Principal of Soramair’s Ammonia Cracker Purifier Unit
The Ammonia Cracker Purifier Unit functions seamlessly to remove un-cracked ammonia and moisture. Molecular Sieves in the two vessels operate in cycles of purification and regeneration. Regeneration involves heating the Molecular Sieves to 200 Deg. C, releasing dry cracked gas. The cooled, purified gas then proceeds through the system.
Setp by step Working Principle of Soramair’s Ammonia Cracker Purifier Unit :
- Cracked ammonia gas from the Ammonia Cracking Unit enters the purifier.
- The gas flows through one of the molecular sieve towers, where the zeolite beads selectively adsorb uncracked ammonia and moisture.
- Purified and dried cracked ammonia gas exits the tower and proceeds to your application.
- Once saturated with impurities, the tower undergoes regeneration.
- The regeneration vessel is isolated from the gas flow.
- The molecular sieves are heated to 200°C, desorbing the captured moisture and uncracked ammonia.
- Desorbed impurities are vented through the exhaust lines.
- The regenerated tower cools down and prepares for another purification cycle.
- The valves automatically switch, directing the gas flow to the now-regenerated tower while the other undergoes regeneration.
Advantages of Soramair’s Ammonia Cracker Purifier Unit
- Enhanced Cracked Ammonia Purity: Guarantees dry, uncontaminated gas for maximum efficiency and optimal results in your downstream applications.
- Improved Process Efficiency: Eliminates the need for additional drying equipment, streamlining your production process and reducing overall costs.
- Reliable and Long-Lasting: Robust design and high-quality components ensure years of dependable operation with minimal maintenance requirements.
- Compact Footprint: Requires minimal space compared to traditional ammonia cracking systems.
- Compact Footprint: Requires minimal space, making it ideal for integration into existing facilities.
- Fast Delivery and Installation: Ready for dispatch within 45 days of order confirmation and our expert team offers seamless installation and commissioning.
Invest in Soramair’s Ammonia Cracker Purifier Unit and unlock the full potential of your cracked ammonia with reliable, cost-effective purification. Contact us today for a free consultation and discover how our technology can optimize your industrial operations!
Explore More Products

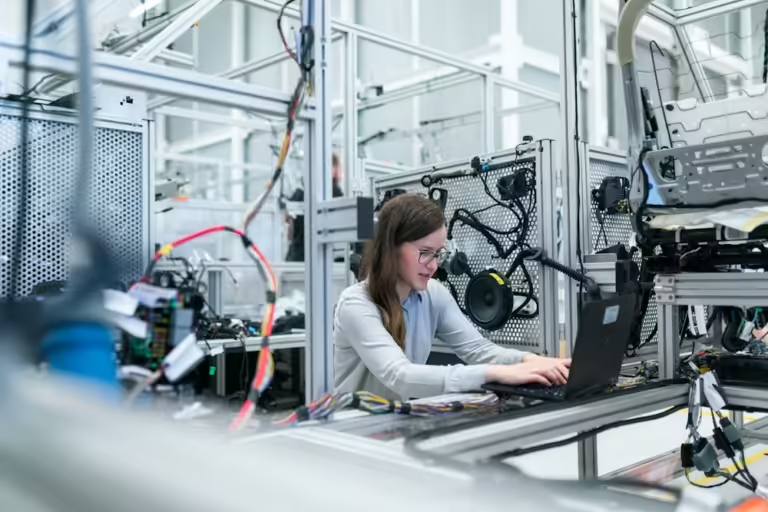
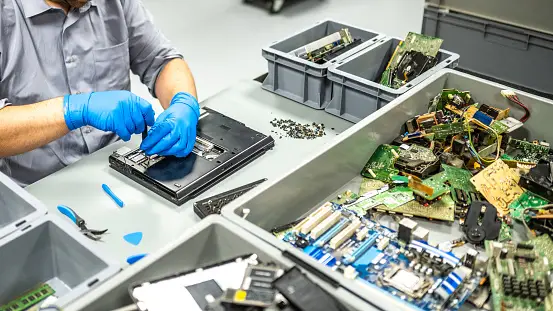


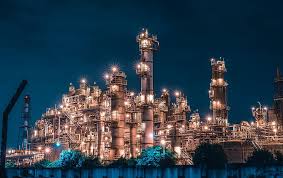
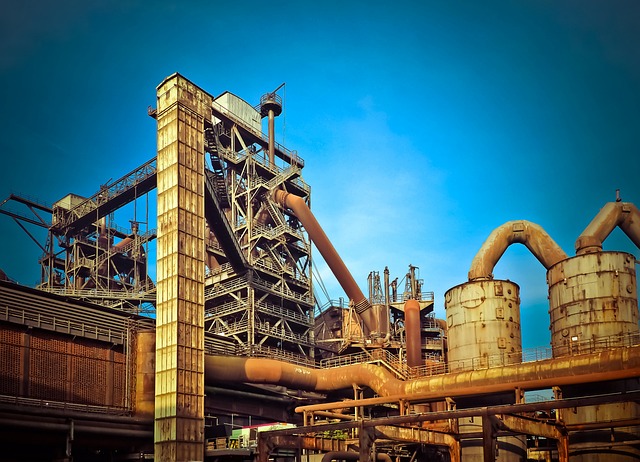

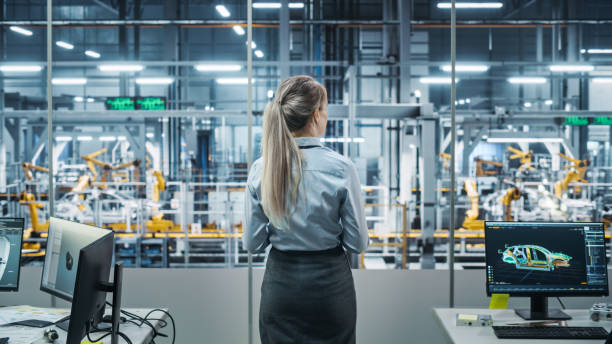
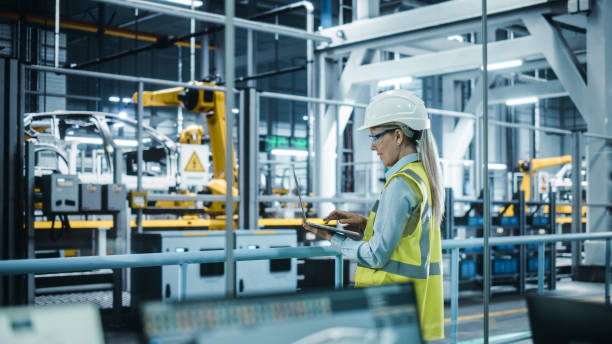

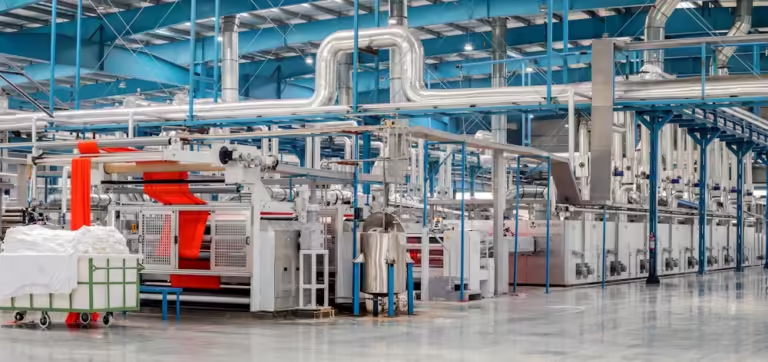